In this blog, we will introduce, how we set up parameters on VFD and configure in Mach 4. In the blog before – CNC Lathe spindle motor – part 1 [setup&wiring] we presented the mechanical and electrical part of the project on how to CNC Lathe spindle motor setup and wiring electromotor and VFD. If you had problems with configuration in Mach 4 in the description you will find out all information for the proper setting.
Table of Contents
VFD parameters configuring
Variable frequency drive (VFD) drives an electric motor by changing – varying the frequency and voltage supplied to the electric motor. For operation, we want functions: ON/OFF motor, control speed, and direction CW – CCW. All these functions can be controlled via PoKeys57CNC.
For the Lathe spindle and our needs, we decide to have around 2000 Rpm. So 2000 rpm is the starting point to calculate the rpm and frequency and then set up on VFD. So in calculation with the frequency we decide the max frequency for the electric motor is 70 Hz, 70 Hz for permanently working is the upper limit and 30 Hz for lower limit- for permanently working. The max. Rpm (1918 rpm) is fine we have a deviation but we use the manufacturer directions (electric motor) for permanently working frequency (Hz). Calculated rpm and frequency we used to set a VFD and configure in Mach 4.


VFD function parameters setting
So we calculate the Rpm. Rpm working area is enough for our needs and efficiencies of our CNC Lathe machine. VFD setting parameters. For correctly working we must set three parameters on VFD-INVT GD20-0R7G-2S-EU. Correctly wiring and setting parameters is important for proper and easier Configuration in Mach 4.
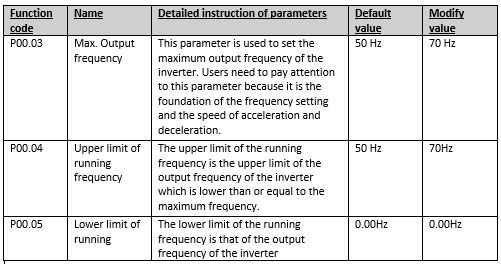
Configuration in Mach 4
Starting with setting Output Signal, to set ON/OFF electric motor and direction CW/ CCW.
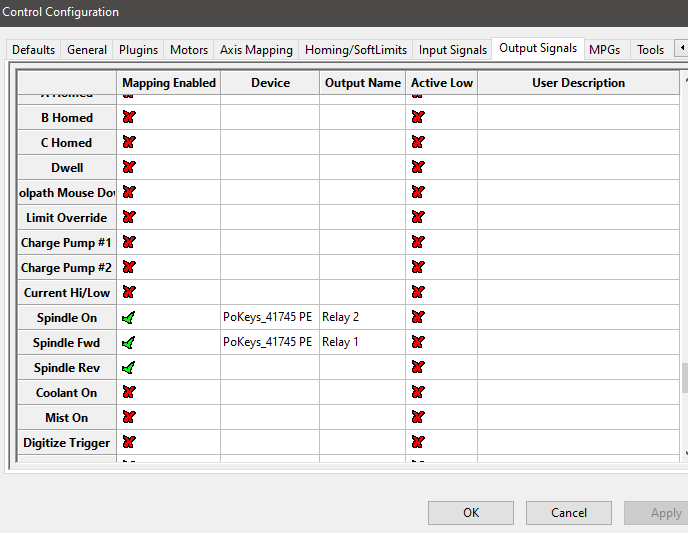
Control Configuration
– PoKeys plugin configuration. Setting Pin17 (0-10V) for control speed (varying the voltage). Varying the voltage on the CNC controller- Varying frequency on VFD and Varying speed- rpm on the spindle.
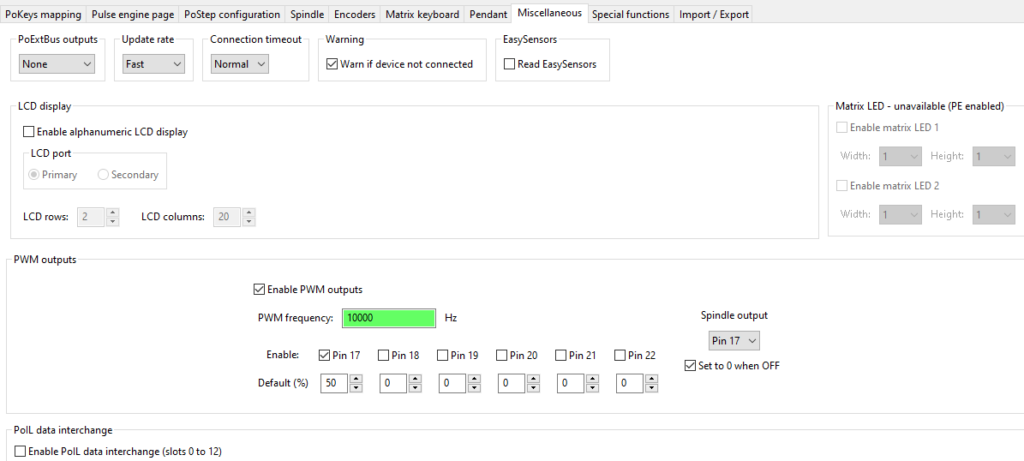
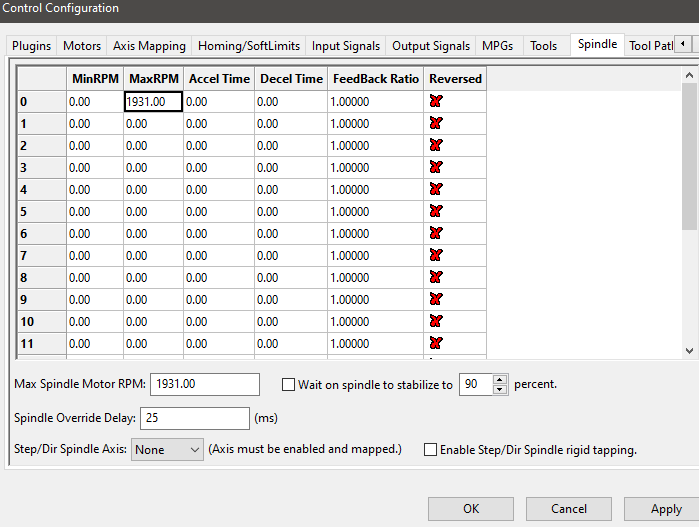
CNC Lathe Spindle synchronization
So, we set the machine in operation, and the settings are fine to start turning and drilling. If we want to make thread cutting on the machine, we must synchronize the spindle. CNC Lathe thread cutting requires Spindle speed synchronization, which means spindle RPM-s must be synchronization with machine linear movement.
To archive this, the CNC controller needs to read feedback signals from the Lathe spindle to gain information at which the RPM-s spindle rotates.
For this purpose we used Optocoupler, Optocoupler – Index is a sort of sensor that would read spindle RPM-s.
In the upper photo, we can see RPM-s (1931rpm)- we talk about (1918 rpm), and set the VFD frequency. So We have a small deviation between the calculated value and the real value on the machine. Can be more faults:
Pulleys are not incorrect ratio – pulley dimension – dimensional deviation.
VFD frequency varies.
Wiring diagram – Index – Pokeys57CNC
In the photo below – is the wiring diagram for the connection Optocoupler with Pokeys57CNC via Adapter Board 10 -10.
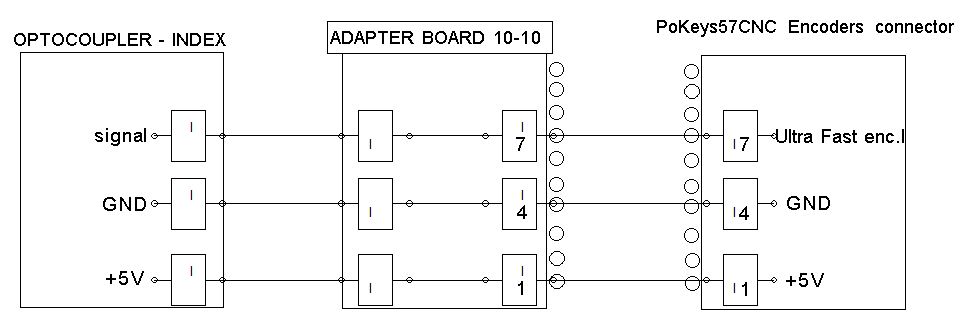
CNC lathe spindle Index – settings
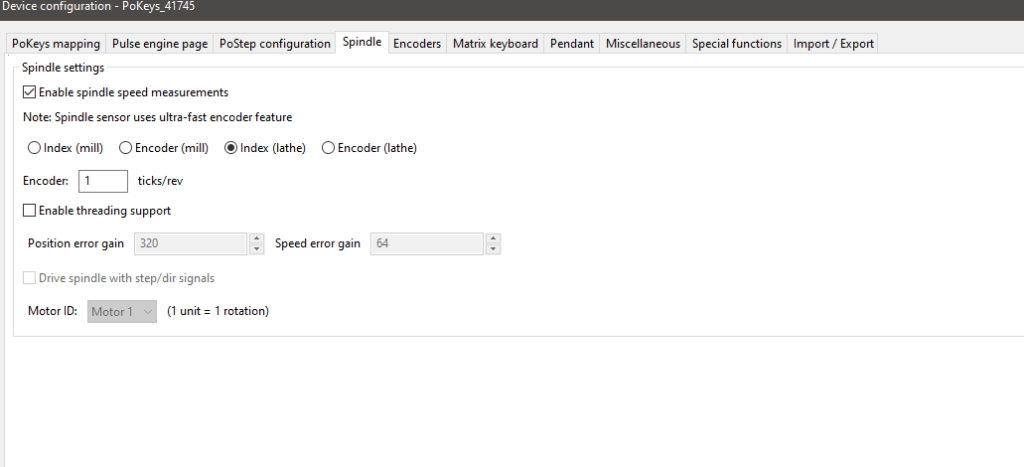

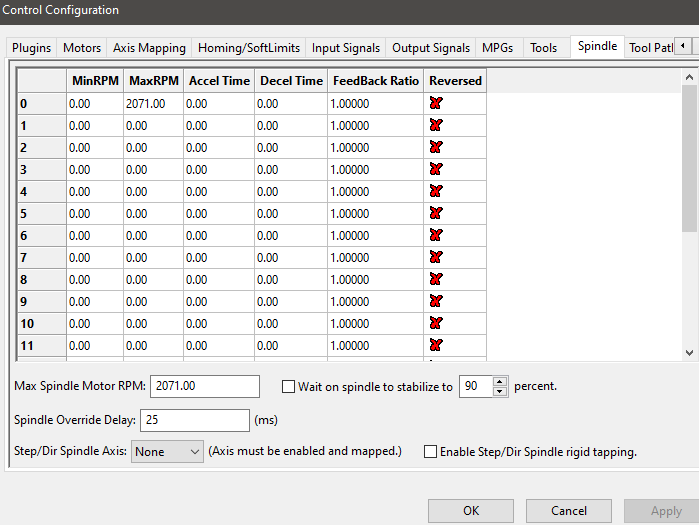
CNC Lathe turning – test part
The photo below – CNC turning a test part. The turning was fine and the machine work properly.
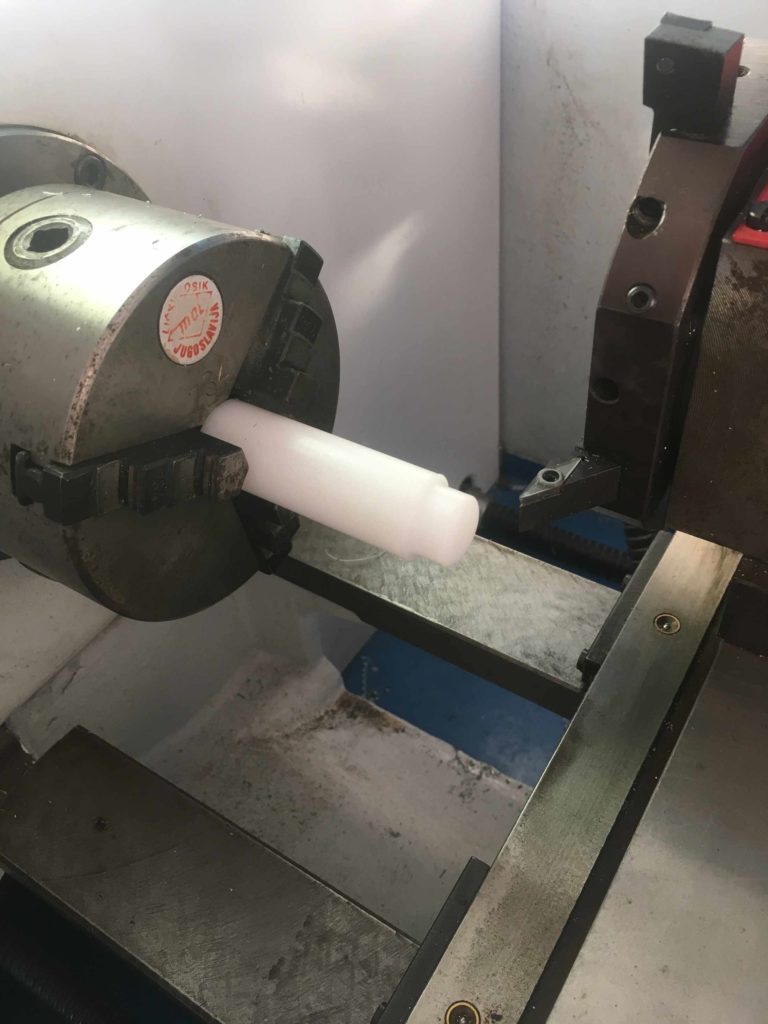
More about
PoLabs web page
For more information about step by step guide PoKeys57CNC and Mach 4
More information about Pokeys I/O devices
Here is a complete explanation about the stepper motor driver.
Please also check our latest blog posts and products. It can help you to improve your machines or get some ideas on how to even make them better.
- Bipolar stepper motor driver – PoStep25-256
- Homing sensor
- Torch height controller – THC
- 4th axis for CNC
- Introduction to CNC hardware – electronics
- Plasma cutting equipment
- What is CNC plasma cutting
- CNC plasma floating head
- Plasma cutter troubleshooting guide