With CNC machines, one can assume the absolute accuracy as high as the control shows. Sometimes the theoretical resolution can be in fractions of the microns. But is it also as precise in reality? How does backlash compensation work?
Where does the inaccuracy of the machine come from?
There is more than one cause of the possible inaccuracy in the CNC machine. Usually backlash is the one that most people first think about but there are multiple other factors to consider. Below is the picture of one of the machine axis. All the critical components are marked. The common knowledge is that the backlash comes from looseness between ballscrew nut and ballscrew itself. But the inaccuracy of the machine can be the result of:
- Backlash between the nut and the ballscrew
- Loose fixed bearing nut – it preloads the angular contact bearings in the fixed support bearing so there is zero play
- Backlash in the coupler which can be poor quality and does not transfer motion and torque very well
- Inaccurate microstepping that results in non linear rotary motion in relation to step pulses
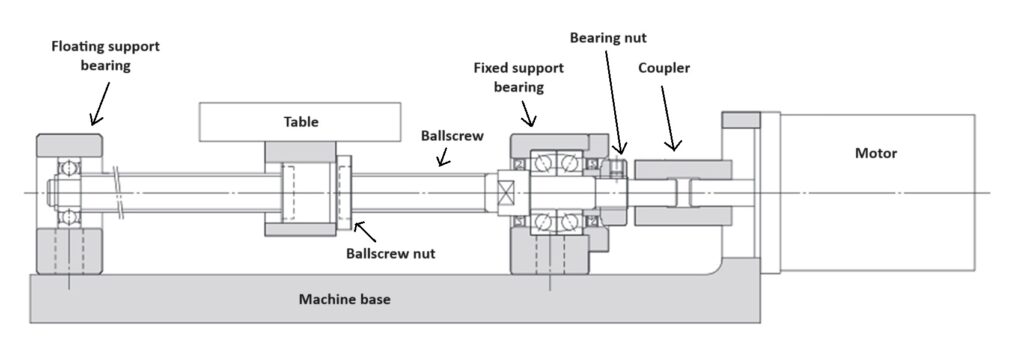
Mounting of the ballscrew is very important and the quality of all the components in the picture is essential for the best performance of the machine. It doesn’t help you much if you buy the best ballscrew with C3 accuracy class if you use inappropriate fixed support bearing. It is as important as the ballscrew which is why new such bearings cost real money. If you buy cheap BK12 support bearing they usually have regular “deep groove” ball bearing inside and it can add as much as 0.05mm of backlash from the beginning not including all the other factors.
Mechanical components and quality of assembly is essential and backlash should be first eliminated here.
How to measure backlash?
Backlash in measured with dial indicator. The axis is driven in one direction and after stopping the position of the axis and indicator is reset to zero. Then the axis is driven in other direction until the pointer on the dial indicator moves. The amount of backlash is then the value of the axis position on the control minus the amount that the indicator has moved.
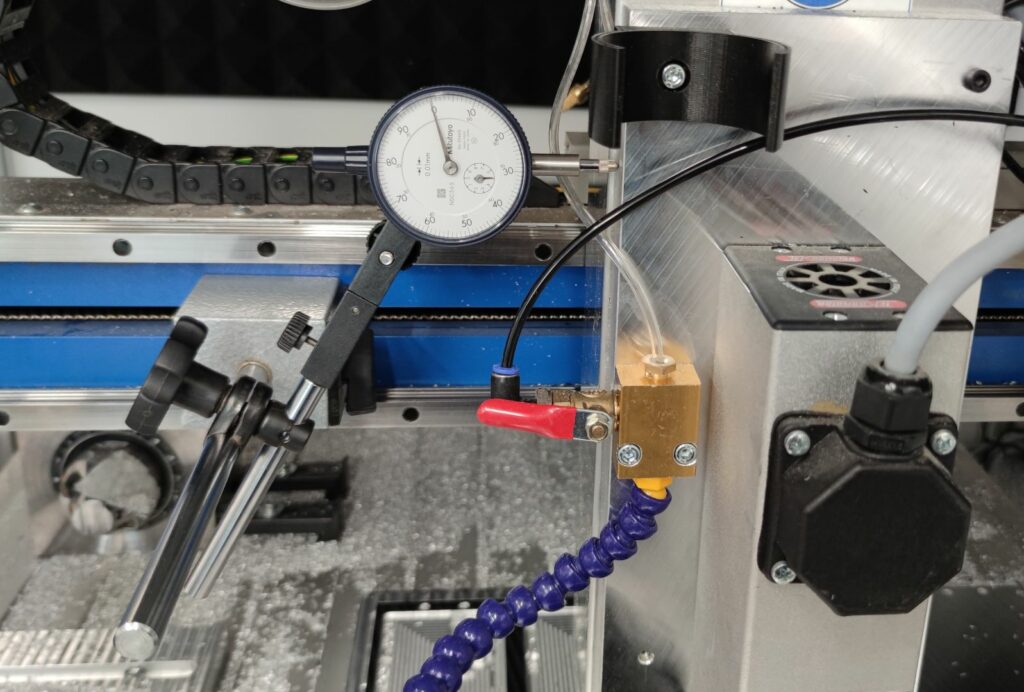
The backlash that we measured is the total backlash of the system including the nut, ballscrew, bearing, coupler and the motor inaccuracy. The usual values are below 0.1mm. The higher values are usually the result of the loosened bearing nut or coupler. Even the cheapest components should result in the values of backlash below 0.05mm.
How to compensate the backlash
We can compensate for backlash in software. Mach4 has setting of backlash compensation that will minimize the amount of inaccuracy of your machine. The values of backlash that can be compensated should be below 0.15mm. If you have more backlash than that, you should first correct mechanical components first.
For mechanical fixes you have more options:
- Replace the nut on the leadscrew with anti-backlash nut
- Replace the thrust bearings in fixed support bearing
- Tighten the bearing nut
- Replace the work coupler or tighten it
- Replace the ballscrew nut or the balls of the mechanism
Mach4 backlash compensation
For electronic compensation in Mach4, you need to enable the backlash compensation in plugin. The acceleration should be left at 1. Next step is then to open the “Control” window for Mach4 settings and enter the amount of backlash for each axis. The regular acceleration of the axis should then be lowered in in order to not lose steps. The backlash compesation acceleration is added onto the regular axis acceleration so total acceleration should not be too high in order for motor to properly follow the step input.
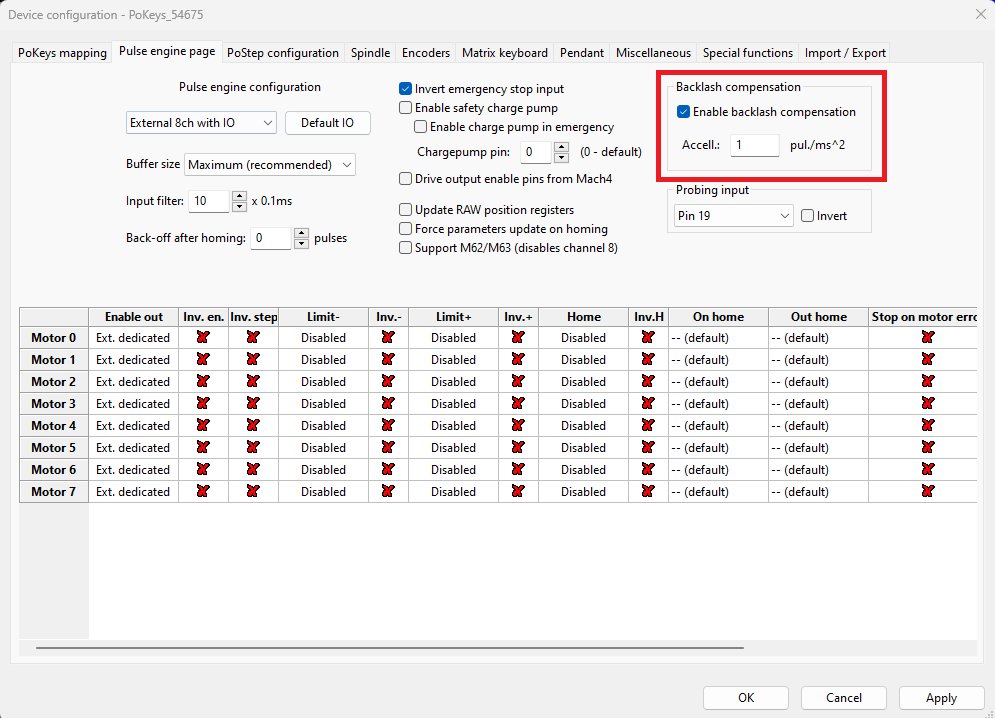
The Mach4 backlash amount is in default units for your machine (in our case mm).
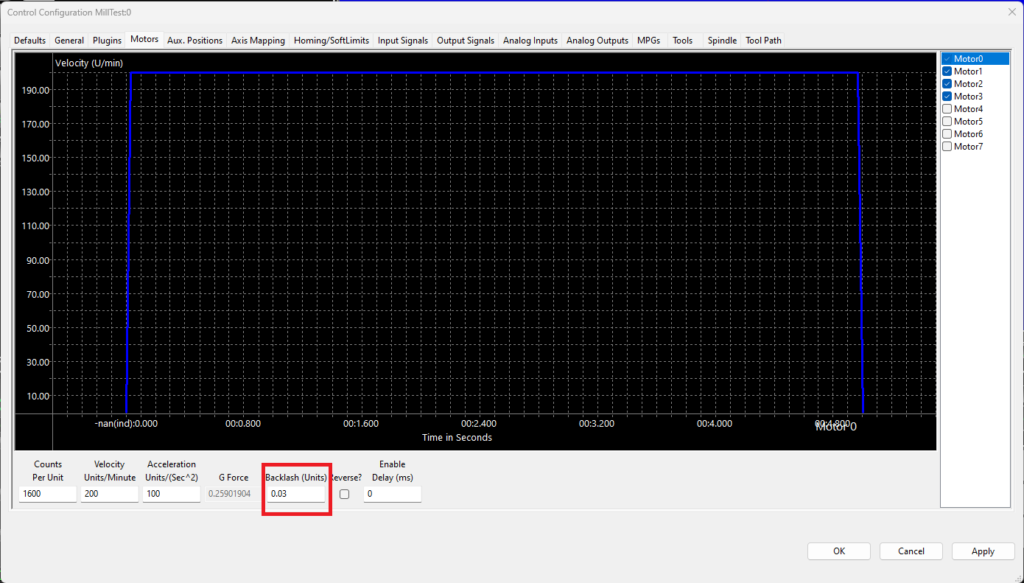
Mach3 backlash compensation
Since backlash compensation in Mach 3 is not directly accessible, you need to open PoKeys application an configure it in Pulse engine menu. Backlash width should be configured as number of pulses divided by 2. Acceleration should be left at 1 and max compensation speed should be set according to your machine capabilities. That speed is added to the motion, generated by Mach 3 and should be set up so the machine doesn’t lose steps.
Benefits of compensated and corrected backlash
For high toleranced parts, the machine has to be very accurate. That way you can achieve the precision that you require. Software backlash compensation is free and can enable you higher precision so it is very vise to spend time and learn the capabilities of your machine and make it better. That way you can also know where are the limitation of your machine and how can you make it better if the future if you decide to upgrade some individual components.
See also our other blog posts about CNC machines, upgrades and use cases for our products.