Do you have a project that demands position control of stepper motor or servo motor? Our easy to use PoKeys devices and PoBlocks programming software enables you to add position control with other peripheral to any custom project.
What do we want to achieve with motor position control?
The project requred motor position control of the servo motor. It was used in an art exhibition to rotate a exhibition object. Every second, it had to be rotated for 6 degrees, so every minute, full circle was achieved. All the electronics had to be packed in a plastic box with mains connection and connection to the motor. With closing the switch there had to be a small (10s) delay until the motor starts turning automatically.
How do we define the hardware needed?
The selected motor was 1000w AC servo motor with appropriate servo drive which had STEP/DIR control. For connecting PoKeys57U to the servo drive, adapterPNPN was used for its optical isolation. That may not have been neccessary since servo drive already includes opto-coupled inputs but better be safe than sorry.
How do we program the motor position control?
All the settings were done in the PoKeys software under the main window and the “pulse engine” page. The enable pin was set up as digital input in the main page. Then under “Pulse engine” page the 3ch internal pulse generator was selected. Note that the internal motion controller has predefined output pins and not every pin can be selected.
Then all the speeds and accelerations were set to appropriate values and enable pin was selected. The hardware could then be tested with manual jogging of the motor.
Program for motor position control is very simple. Clock source is wired to the “up counter” that makes a delay which causes the 5 second delay at the beginning after power up. Then both signals are wired in AND gate which after initial 5 seconds trasfers clock pulse to the next counter. That counter then counts indefinitely and is wired in the multiplier to get the exact number of steps per 6 degree rotation of the motor. That signal is then fed into the reference of the axis move to make the motor turn.
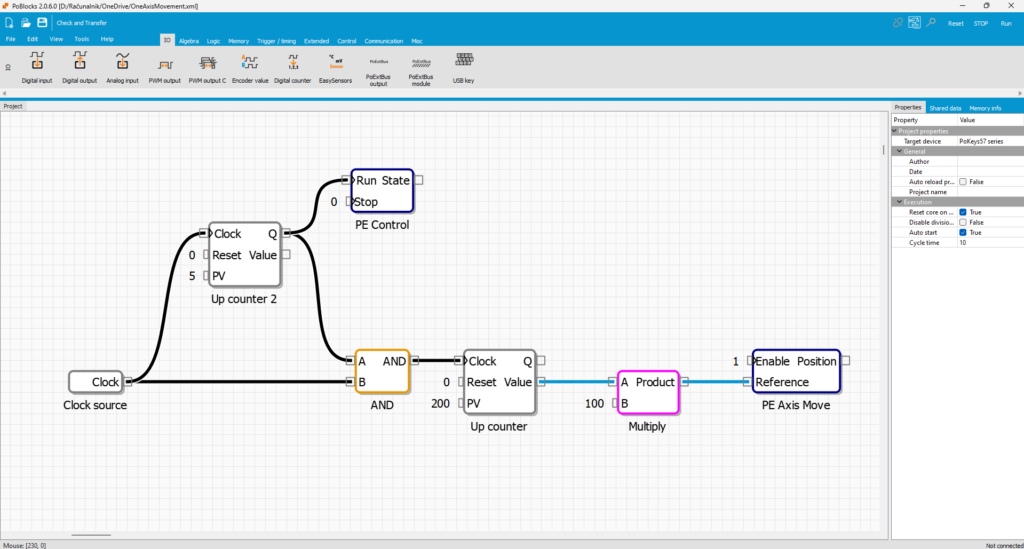
Conclusion
Project was done very quickly thanks to the easy to use PoBlocks software and pokeys device. The PoBlocks enables you to program PoKeys devices easily and learning curve is not as steep as with other systems.